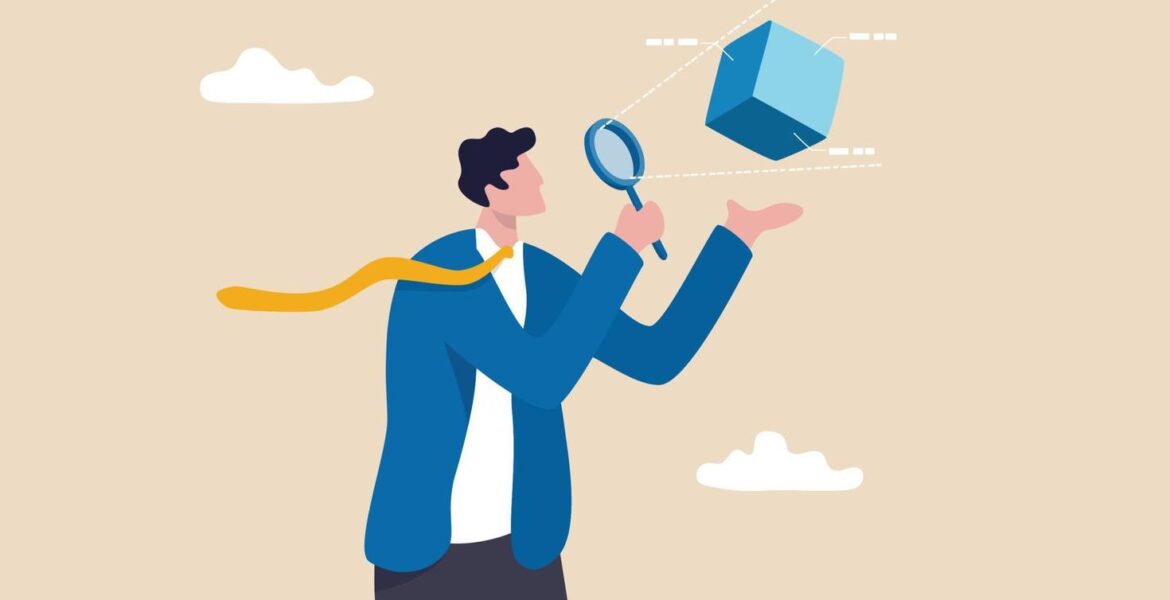
Problem finding and analysis of the production and management system
Diagnostic Models in Production and Management Systems: A Tool for Identifying Issues and Improving Performance in Businesses
In every organization, analyzing and identifying existing issues in production and management processes can lead to significant improvements in performance, cost reduction, quality enhancement, and increased efficiency. Diagnostic models serve as vital tools in this process, helping to identify hidden problems and providing appropriate solutions. These models enable businesses to uncover operational barriers, wasted resources, and latent issues, and optimize systems, processes, and performance for overall organizational improvement.
Our consulting team is ready to assist your business with advanced diagnostic models to identify issues and find effective solutions for improving your production and management systems.
Different Diagnostic Models in Production and Management Systems
In the diagnostic process, several different models and methods are available to help businesses identify problems and weaknesses in their systems. Here are some of the most important models and techniques:
1. Cause and Effect Analysis (Fishbone Diagram or Ishikawa Diagram)
This model, also known as the Fishbone diagram or Ishikawa diagram, helps identify the causes of problems in a specific process. Visually, the diagram categorizes various factors that could contribute to the problem (such as people, machines, materials, methods, and environment). This allows businesses to pinpoint the root causes and seek improvement solutions.
Application in Businesses: This model helps businesses analyze complex issues like quality reduction, decreased production, or management problems, and identify their root causes for effective resolution.
2. Gap Analysis
Gap analysis examines the differences between the current state and the desired future state. In this model, the current state of systems and processes is assessed, and then goals and future expectations are established. The gaps between these two states are identified, and actions are proposed to bridge these gaps.
Application in Businesses: This model helps businesses identify the distance between their current performance and desired goals, evaluate resources and processes, and design improvement plans to close the gaps.
3. The 5 Whys
The 5 Whys model is a simple yet effective method for identifying the root cause of problems. In this model, you simply ask “why” a specific issue occurred. After answering, you ask “why” again, and repeat this process up to five times until you reach the core cause of the problem.
Application in Businesses: This model is useful for identifying both small and large problems in organizations. By using this model, businesses can uncover the underlying causes of issues in processes, production, or management and implement corrective actions.
4. SWOT Model (Strengths, Weaknesses, Opportunities, Threats)
The SWOT analysis model is used to assess the internal strengths and weaknesses, as well as external opportunities and threats of an organization or specific process. This model helps businesses identify internal strengths and weaknesses and understand external factors that may affect them.
Application in Businesses: This model assists organizations in identifying their weaknesses and external threats, allowing them to develop strategies to improve performance, productivity, and mitigate risks.
5. FMEA Model (Failure Mode and Effect Analysis)
FMEA is a systematic technique for identifying potential failures or faults in a system or process and assessing their effects. In this model, potential risks are first identified, and then their impact on processes, production, and quality is evaluated.
Application in Businesses: This model helps businesses recognize potential risks and issues in their production and management systems and take preventive actions before problems occur.
How Our Consulting Services Can Help You
Our consulting team uses advanced diagnostic models and production and management system analysis techniques to help businesses identify issues and find effective solutions for improvement. Our services include:
• Comprehensive and Detailed Evaluation of Systems: We carefully assess your processes and use various diagnostic models to identify problems and opportunities for improvement.
• Customized Solutions for Issue Resolution: Based on the analysis, we provide practical and tailored solutions for improving your performance.
• Guidance on Implementing Changes and Improvements: Our team supports you through the implementation process, ensuring that the necessary changes are executed efficiently and effectively.
• Ongoing Support and Progress Monitoring: After implementing changes, we provide continuous monitoring and support to ensure sustainable improvements and long-term success.
Take the First Step Towards Improvement
If you want to identify the issues in your production and management systems and use advanced diagnostic models to enhance your business’s performance, our consulting team is ready to assist you. Contact us today and benefit from our professional consulting services.